阅读: 2,647 次
一、前言
流程型生产企业的生产过程,通过信息化展示后发现,是一个连续性、大滞后、大惯性的数字化处理过程。伴随有物理、化学反应等过程,生产工艺、生产工况非常复杂。即使是相同类型企业,其生产工艺、生产工况也会存在较大差异。在生产工艺方面,相关生产参数之间存在非线性持续变化且相互影响的特性。 为了满足处理上述状况的需要,针对性的解决问题,所以在设计智能化系统时应考虑以下关键核心技术。
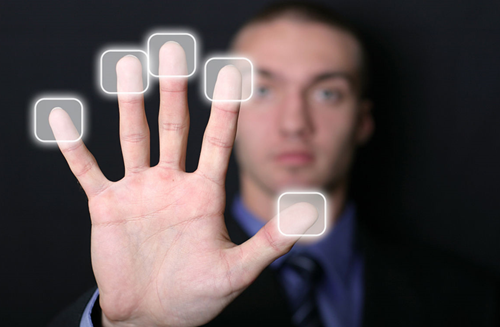
二、神经网络技术
1、神经网络分类
神经网络技术分为前馈神经网络、反馈神经网络两个分类。
前馈神经网络(Feedforward Neural Network),简称前馈网络,是人工神经网络的一种。在此种神经网络中,各神经元从输入层开始,接收前一级输入,并输出到下一级,直至输出层。
反馈神经网络是一种反馈动力学系统。在这种网络中,每个神经元同时将自身的输出信号作为输入信号反馈给其他神经元,它需要工作一段时间才能达到稳定。
2、前馈神经网络
前馈神经网络技术的应用,目的是满足系统控制目标参数可以即时计算出发展趋势曲线及预测分析。
典型的RBF(Radial Basis Function)网络由三层组成:一个输入层,一个或多个由RBF神经元组成的RBF层(隐含层),一个由线性神经元组成的输出层。如下图:
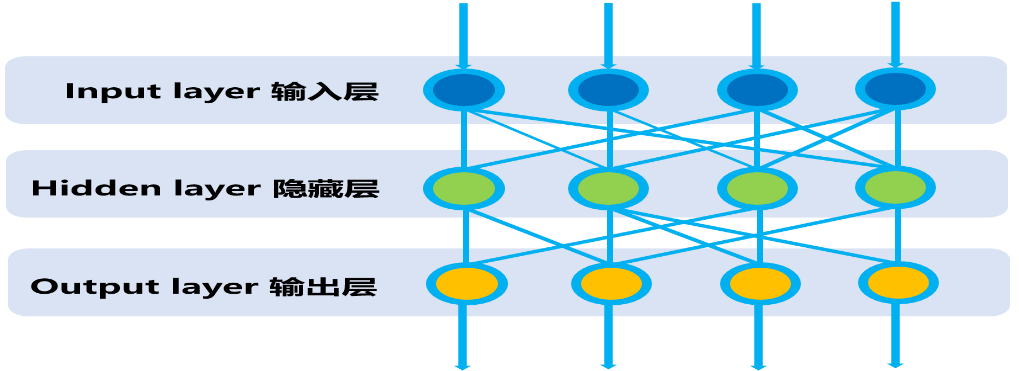
3、反馈神经网络
反馈神经网络可以认为就是智能化系统要重点解决的。通过软件来模拟反馈神经网络。
4、联动应用
前馈神经网络以物理特性为主导,真是反映客户现实数据。提供参数数据、神经元趋势计算、分析等。
反馈神经网络抽象特性为主导,通过必要的数学模型计算,动态对冲设备调节量,并向最终的设备发送可执行的调节量指令。
三、智能模拟技术
智能模拟,顾名思义,模拟人的行为。就是模拟产线最优秀操作工的产线控制操作行为。
智能模拟,需要构造多层嵌套智能控制模型,以实现对人工操作行为的全息模拟,而不是简单的停留在用人工智能技术简单的分析输入输出等相关参数的数值关系层面。通过机器感知、机器预判的超前控制计算,大幅调节和小幅逼近相结合的方式让生产线运行状态逼近最优。
生产环境在工况相对稳定时,智能化系统应识别为稳定状态,此时的实际控制效果与传统的模糊控制人工智能控制效果类似,主要由小幅逼近方式逐渐逼近最优控制目标。
在工况发生大幅波动时(系统外部干扰因素所致)系统应识别为不稳定状态,此时将以机器感知、机器预判模型为主要依据,预测被控参数的未来短期变化,实现预测式大幅调节。这种预判,由于不能全面预测外部干扰因素的所有可能变化,因此存在少数误判可能,此时可以根据实时数据波动情况来对比曾经作出的预测值,通过补偿模操作控制进行适量补偿修正。 需要强调的一点,基于模糊数学理论的机器学习解决不了模拟人的行为。若你的技术路线基于此,则注定竹篮打水一场空。
四、实时数据清洗技术
智能化系统运行好坏的前提是产线数据采集的干净程度。事实上,生产产线每分每秒产生的数据,均掺杂着一些脏数据。传感器的瞬间故障,就会造成工业控制中很多采集到的数据可能是无效的、不可能的,这样就会导致数据比较脏。发生脏数据的原因很多,也难以一一彻底清除。无效的数据控制信息,可能对生产作业系统产生副作用。把“脏数据”清洗干净,或者把“不成型”的数据成型,再非常准确的反馈到生产设备的控制上,才能有卓越的控制效果。所以,非常有必要对产线数据进行精心的清洗!
数据的清洗工作一般采用实时数据库的数据处理机制,对数据进行ETL处理后加以应用,数据处理效率达到毫秒或者秒级。若有必要,再把这些数据写入关系数据库。 实现数据清洗的技术方式很多,无论采用什么技术方式,均要以性能目标的定位关联起来考虑。性能目标定位的核心就是系统需要的执行效率,是毫秒级还是秒级!大部分应用秒级就可以了,但有一些应用必须要到毫秒级!
五、控制数据关联匹配技术
控制数据的大延迟、大滞后,是流程型生产企业普遍存在的现象。生产线的不同设备相互之间总是存在着千丝万缕的必然联系。从这些设备采集到的实时数据,由于滞后等原因,相互之间的关联可能不在一个时间轴上。而产线很可能存在多个时间轴。生产设备之间的数据大滞后、大延迟也可能不是固定。
所以,找到时间轴的焦点,就是准确找到数据大延迟的时间,各个设备数据大延迟的时间。
数据大延迟的时间,往往不是固定的,但却遵循着产线特定的规律。同一产线,时间延迟也会存在动态偏移,时间的偏移也存在着特定的规律。实际经验来看,找到数据大延迟的时间及偏移规律,就找到了控制数据关联匹配的核心。剩下的工作就变得简单多了。 只有把多设备、多控制点数据结合数据大延迟时间及偏移规律,按照业务合理对接起来,让设备不同的时间点上的数据相互关联,然后再判断出设备指令方向,再计算对冲量值,就能发挥设备最优特性。
六、平台化设计思想
针对一条生产线开发设计完全符合生产要求的智能化控制系统,可行,但不推荐这样的做法。
设计的出发点,应该是站在平台化的思想基础上。就是运行的系统与工艺的描述彻底分离!
运行系统与工艺过程、工艺参数不能分离,只能适用单一的生产环境,无法规模化复制到其他企业或者其他的领域中。
另一方面,实际实施过程中,大概率不可能一步到位的实施完所有需要控制的节点、或者控制目标,需要逐步完善。若需要循序渐进,逐步完善,那么牵一发而动全身的灾难是无法控制的。长久来看系统实施,注定是失败的。
鉴于此,以平台化设计思想的智能化系统,就显得优势充分。无论设备改造,或者增加控制节点、控制范围时,无需升级控制系统。只需要完善对工艺流程、工艺参数的完善即可。
运行系统与工艺过程、工艺参数分离后,各自可以独立升级。工艺过程、工艺参数可以作为一个独立的描述文件,如XML方式,或者存放在数据库中。系统运行的基础是工艺过程。工艺参数的描述文件。这样,智能化控制系统就会向越来越稳定、精准的方向发展,同时,适应面也就越来越宽广!
你真的需要这样做!
七、通信协议
1、OPC协议
只要您构建智能化控制系统,OPC协议必不可少。若您的系统没有涉及到这个协议,那基本的判断就不是智能化系统,或者您构造的系统没有生命力! OPC协议是DCS系统与AI系统之间通信协议,是完成驱动设备操作的唯一有效性技术方式。一方面,基于设备的操作系统DCS与AI系统分离,确保了两者独立运行及独立升级。也能确保AI系统应用的广度。
2、UDP协议
若您设计的智能化系统需要向互联网发布动态数据,这个协议是首选。可以在物理隔离的生产网络中构建出于互联网单向通信的数据通道。
UDP协议不是必须使用的。关键看用户的应用需求是不是需要向互联网发布数据。与互联网有关系,则必须使用。
八、安全保护
设计实施流程型生产企业的智能化控制系统,生产的安全问题,必须要在每一个环节中着重体现出来。生产安全没有小事!有了事,就是大事!
系统的预警、报警、边界限制等这些常规机制、措施必不可少。本文无法全面的描述如何做到生产安全,只能点到为止。但有一个可以参考的指标,供大家借鉴使用。就是您的智能化控制系统的代码量对于安全性处理的比例是不是达到了85%以上。这个指标是首要的,更是安全防护的一道金盾。 另外,系统投产后,给出的操作规程是否详尽,也要引起重视。企业老的操作规程与智能化系统之间是否有矛盾的地方,要协助企业调整过来。
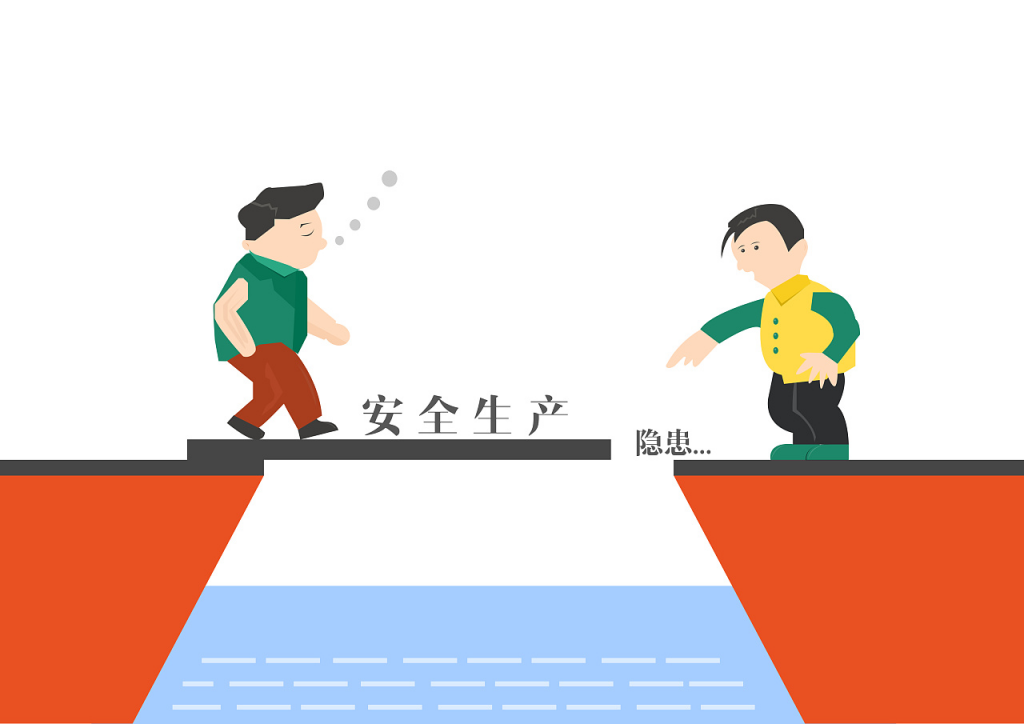
阅读: 2,647 次
交流邮件:suibaohua@ridic.top