阅读: 7,181 次
一. 研究背景
目前,中国流程型生产行业的生产管理方式,正在由粗放型向精细化管理转型,安全稳定生产,节能降耗、减排,降低企业生产成本,已经成为企业管理者的主流意识,也开始进行大胆地实践。
流程型生产企业往往都是重资产类型的企业,设备多,运行状况比较复杂,仅仅依赖人工监管、调度,已经落伍于时代发展的大趋势。而通过信息化手段辅助生产,就可以最大程度的避免因人工操作导致的操作失当,提升操作精准度和及时性,从而提升生产稳定性、降低能耗、稳定排放、最大程度降低生产成本,并确保生产出来的产品质量长期稳定。 很多流程型生产企业实现了自动化控制,装备了精良的DCS设备控制系统,可以通过中控室直接向产线设备发出产线生产调节指令。生产的调节控制已经从现场的人工控制,切换到由中控室操作工通过计算机来实现控制产线生产,实现了人类生产制造的一次革命。
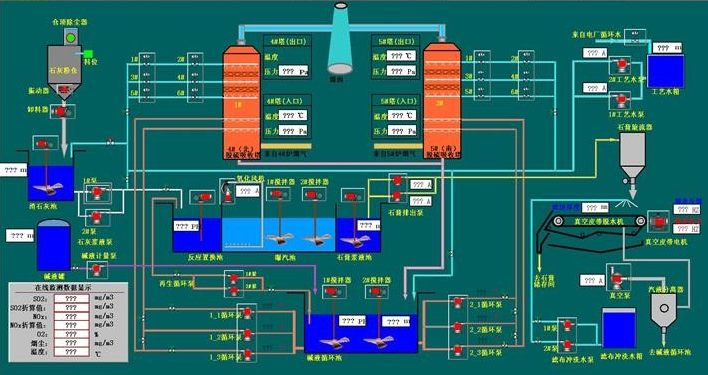
使用DCS系统虽然实现了工业生产的一次革命,但实质上工业生产的控制依然靠人来执行,只是把控制的方式由生产现场转移到了中控室,产线技术革命没有进行到底。
若能够在DCS系统之上,再构建一层智能化控制系统,我们可以理解为把产线的控制调节权交给了计算机,相当于计算机就是一个优秀的操作工在不知疲倦地工作。这样流程型生产企业的自动化控制可能就近乎完美了!
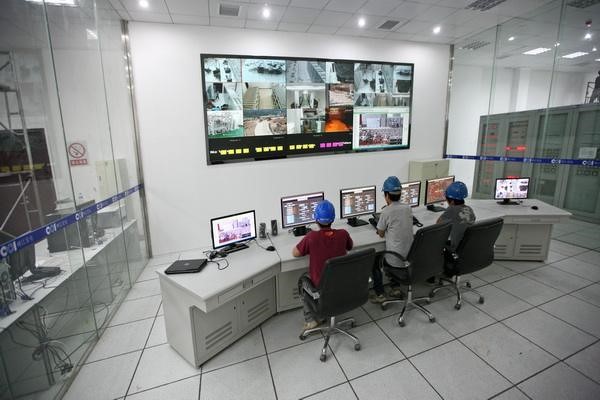
本文的研究重点,就是探讨如何构建流程型生产企业的智能化控制系统,以及各种技术形式的优劣,以达到无人干预下的全自动生产控制效果的目的。同时,让更多的实践者少走一些弯路,更好地促进这个领域的良性发展。
二. 传统控制模式下的缺陷
这里所定义的传统模式,是指流程型生产企业已经部署了DCS系统,并且有足够的执行机构能够被DCS系统用于执行操作指令,中控室操作工通过DCS系统就可以实现对生产控制指令的驱动,从而调节产线的最优化控制效果。若还没有使用DCS系统,或者有DCS系统但缺乏足够的执行机构来支撑,那么我们只能把这种模式定义为“传统的控制模式”了。
传统的控制模式存在以下缺点:
- 人工监控生产线曲线数据变化,人工操作DCS系统。缺点:不能实现通过计算机进行智能化控制。
- 仅仅依靠DCS操作员的经验下达操作指令。缺点:产品质量、能耗、环保指标、环保用料等也随着操作员的经验起伏不定。
- 人的精力有限,优秀操作工的数量有限。生产设备运行状态靠人工控制,无法达到长期最优状态。缺点:有限的能力与无限的产能本身不匹配。
- 人工操作,原材料使用、能耗、环保等指标几乎靠人员经验。缺点:无法实施精准操作,更无法进一步深度优化。
- 产线生产不稳定。缺点:导致无法实施基于工艺深化的PDCA循环,导致工艺深化进程停滞不前,产量、质量难以达到理想状态。
- 管理不当。缺点:每年各种资源的浪费损失15%-30%以上。仅仅依靠管理,又不可能达到减损的最优!
综上所述,流程型生产企业急需进行一场新的技术革命,即通过智能化系统的构建,可以最大化地规避传统模式下的所有缺陷。 于是,基于流程生产制造的工业人工智能技术应用应运而生!