六. 智能化控制系统未来的发展方向
1. 机器学习向机器感知、机器预判发展
通过更高效的神经网络计算,形成机器感知、机器预判神经元群,本着先定性,后定量的原则,产线各个执行机构根据控制模型,动态计算出瞬时的操控指令。
产线设备之间运行达到瞬间的平衡性、合理性,相互影响反馈参数。
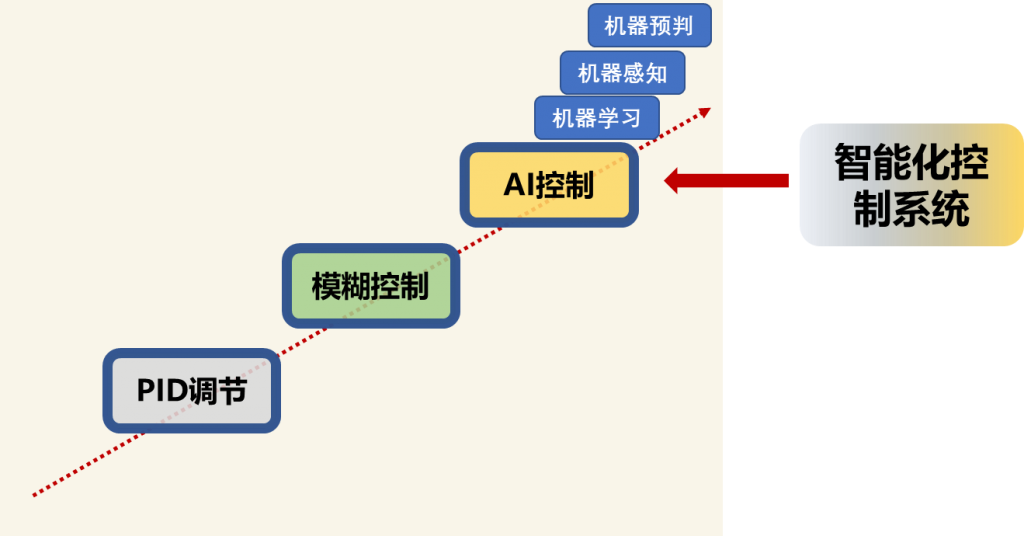
2. 控制模型由模糊化向抽象化发展
模糊控制需要庞大的操控指令数据库支撑,系统性能等因素无法确保。很多产线的控制往往需要在200ms以内就得发出调节指令。所以控制模型的建立不建议再使用操控数据库的技术路线。
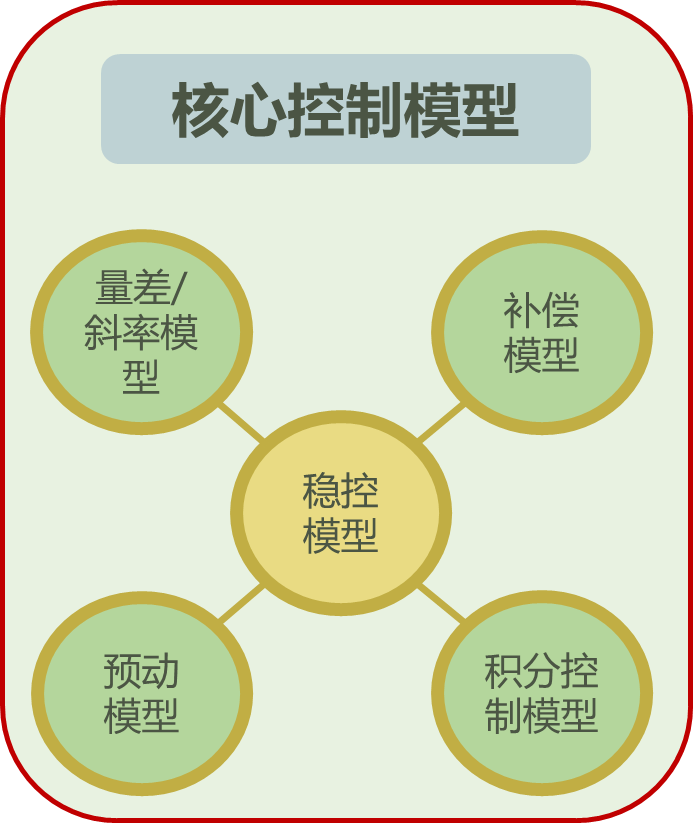
图中5个控制模型,就是更抽象化的控制模型。当然,更需要产线大数据的支撑。产线大数据通过时序数据库来负责承载,抽象模型依据时序数据库的数据来进行高效率的计算。
模型的计算效率均可以确保在80ms以内。
3. 控制模型与工艺参数分离
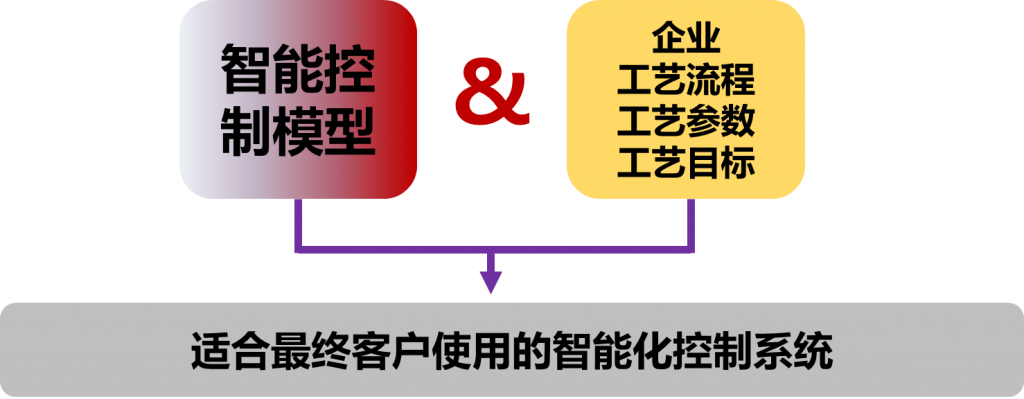
依据高度抽象出来的控制模型,构造出不具备任何行业特色的控制软件。然后,给这个软件匹配具体某个企业具体的工艺流程、工艺参数。最终形成了适合这个企业的智能化控制系统。
这样企业的产线无论如何进行改造,只要调整企业的工艺流程、工艺参数库,那么该企业的智能化系统就永远不落后,极大增强了系统的持久性应用。
4. 微服务群集成
智能化系统要切割为N个微服务,服务器连接、采数、数据清洗、各种模型计算、时序数据、数据分发、数据广播等等,形成系统的微服务计算群。
每个微服务都执行自己特定的专一任务。每个微服务也可以独立升级,独立启停。
所有微服务的运行,形成了产线特有的神经元控制网络。一切都在高效率的有序运行。
若不能分割最小化的微服务,做成一个大服务,那么带来的缺陷过于明显。一方面,升级必须全部停止。另一些方面无法利用操作系统、服务器的性能。
5. 产线工艺智能自我优化
系统为产线工艺工程师提供工艺智能化自我深化的工具。工艺工程师只负责定义工艺深化的目标,其他的工作,智能化系统自我迭代完善,形成全自动化的工艺迭代优化效果。这就是所谓的“专家系统”。
在不影响产线生产产品质、量的情况下,系统根据工艺工程师设定的工艺目标,进入PDCA的不断迭代。
每完成一次迭代优化,工艺工程师必须再重新设定新一轮的工艺深化目标。
在生产设备不更新的情况下,工艺优化总会出现一个瓶颈。这个瓶颈的出现,就是系统再也无法完成新一轮的迭代目标。
6. 单一功能的专用设备越来越多
对于生产线的生产需求,会有越来越多的单一功能装备、设备不断涌现。伴随着各种基于高端、高性能、高可靠性的传感器不断涌现,单一处理某个状态场节点的专用设备、装备也会应运而生。这些装备、设备,会对智能化系统提供更好、更优的控制策略,也一定会对产线的生产质量发生本质的改善。
智能化系统扮演的是产线总体协调、控制作用,不断与单一、专一的特定设备集成是必然的发展趋势。
7. 云控制策略技术路线消亡
云控制策略,天生就是一个不可取的技术路线,缺陷过度明显,安全后果非常严重。一旦出事,智能化系统服务商无法赔偿损失。同时,还承担着较为严重的司法责任。所以,此种技术路线会逐步淘汰。
交流邮件:suibaohua@ridic.top